Precision Tube Standard
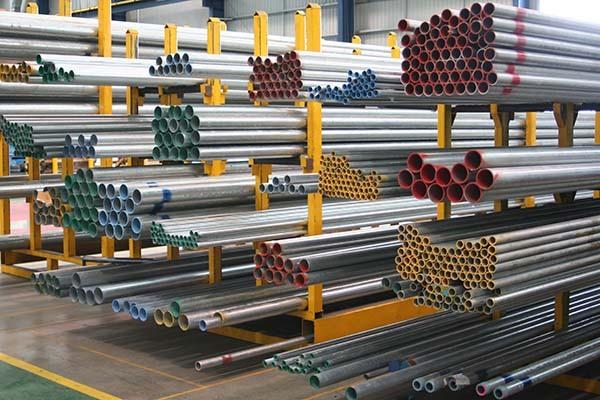
Chemical composition
The carbon equivalent (CE) is determined in accordance with the equation from
AS 1450-2007, i.e. CE = C + Mn/6 + (Cr + Mo + V)/5 + (Cu + Ni)/15
Full chemical analysis to be shown on Test Certificates.
Mechanical Properties
The mechanical tests – yield, tensile and elongation – will be carried out in accordance with AS1391. Prior to tensile testing, the test pieces shall be aged by heating to a temperature between 150°C and 200°C for not less than 15 min.
Elongation results shall be reported on a gauge length Lo = 5.65√So where So is the original cross-sectional area of the test piece before testing.
Test specimens are to be taken longitudinally from a major flat portion of the section.
Test frequency is as per AS 1450-2007.
Finish Coating
RHS and SHS – blue paint.
Pipe – black paint.
Pregal – zinc coated coil with Clearcote coating applied.
Coating Thickness
Painted product – minimum paint thickness of 9 microns
Pregal product – average zinc thickness of 50 grams per square metre per side (Z100).
– minimum Clearcote thickness of 9 microns.
Surface finish
Product shall be free from lamination, surface flaws and other defects detrimental to its use.
-0mm + 15mm (Standard lengths 6.5 and 8 metres)
End Condition
Products are supplied with mill cut ends with burr held to a minimum. End coding is applied in accordance with AS/NZS 4496:1997.
Straightness
The maximum permissible variation from straightness shall not exceed: – Specified length 500
Corner radius
Outside corner radius is 2 x gauge ± 0.5mm, i.e. 2t ± 0.5mm
Squareness of sides
Maximum permissible is 90o ± 1o
Twist
Maximum permissible is 2 mm + 0.5 mm/m length
External dimensions
RHS and SHS – ± 1%
CHS – + 0.1mm, – 0.3mm
Gauge
The maximum variation in thickness of all products will not exceed ± 10%.
Concavity/Convexity
Maximum 0.8% or 5mm, whichever is greater
Cold flattening test piece
The test piece shall be taken in the form of a cross-section from one end of a finished length of a circular tube which contains a longitudinal weld. The length of the test piece shall be not less than 40 mm. All burrs shall be removed before testing. The test piece shall be cut in the transverse direction.
Straightness
Profiles will be supplied to a straightness of Imm in 500mm measured as follows:-
The straightness will be calculated by measuring the horizontal deviation (a) over the ordered profile length (L), i.e. (a) L/500.
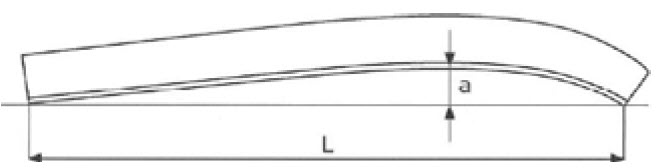
Corner radius
Corner radius is 2 times gauge plus or minus 0.5mm
Squareness
The maximum out of squareness of a profile will be plus or minus 1.5 degrees.
Twist
The maximum angle of twist of a profile (a) will be 1 degree in 1 metre.
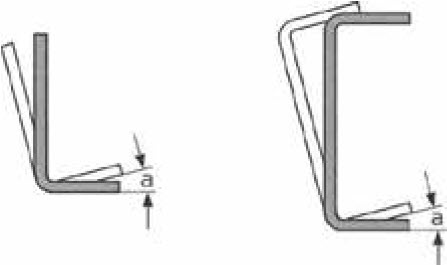
Flatness of sides
The flatness of any side (a) will be limited to less than 0.8% of the width of that side or 0.5mm, whichever is the greater.
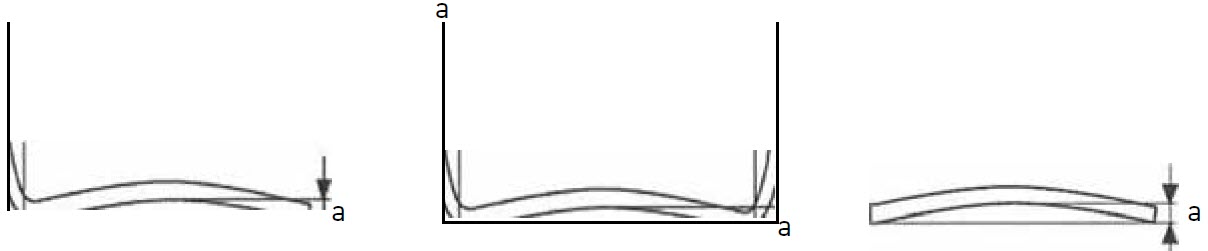
Dimensions
The maximum variation in leg and web dimensions of angles and channels will not exceed 1.5mm.
For the maximum variation in width of flats refer section 16 below.
Width of flats
The variation of the width (W) dimension of flats, where (t) is the designated thickness, are as
follows:-
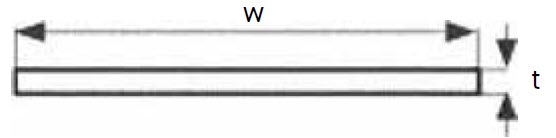
Gauge
The maximum variation in thickness of all profiles will not exceed plus or minus 10%.